Technologies
Casting Technology
Iron Casting
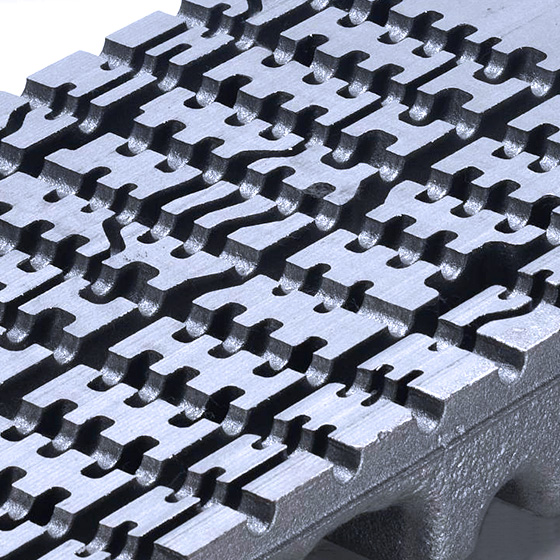
We realize highly reliable manufacture, made possible by our product-specific production systems and streamlined operations.
Capable of forming iron in any desired shape, casting – as the technology vital to the manufacture of parts and components mainly for automobiles and construction machinery – has supported the development of major Japanese industries. As times change, ever higher performance is expected of cast iron parts and components in terms of light weight, compactness, functionality and eco-friendliness. In order to meet these customer needs, Koyama has established its own advanced production system while continually enhancing its technological strength. The results are our proud cast iron products with world-leading performance capabilities.
Examples of Manufacturing Processes
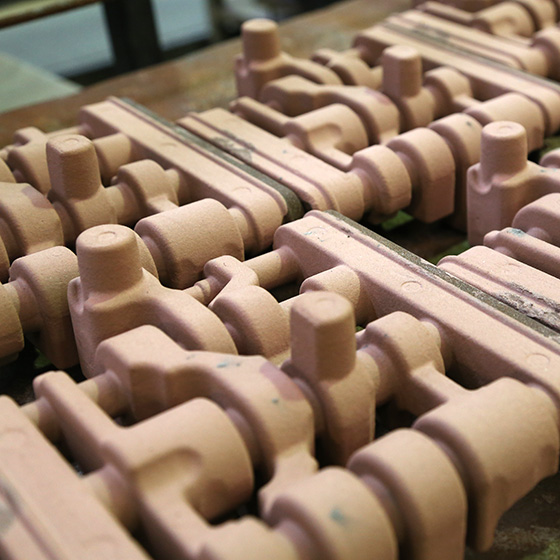
Melting
We have melting facilities such as electric furnaces and cupolas, out of which we choose and use the most suitable one according to material properties and required cost performance. We discharge the optimal molten metal after analyzing and adjusting its 48 different components using a CE meter and an emission spectrophotometer.
Molding of the master mold and core
This is the process to make the master mold by pouring molten metal into the desired product shape, and to mold the core which will become a hollow cavity that forms the interior of the cast product. This process requires the highest possible precision and strength. Our originally developed contactless core has realized the casting of parts and components with extremely complex shapes.
Pouring of molten metal
Our highly efficient and energy-saving automated facilities enable us to pour molten metal into the mold – safely, accurately and efficiently. We can supply cast products of the highest possible dimensional accuracy thanks to the use of state-of-the-art casting machines.
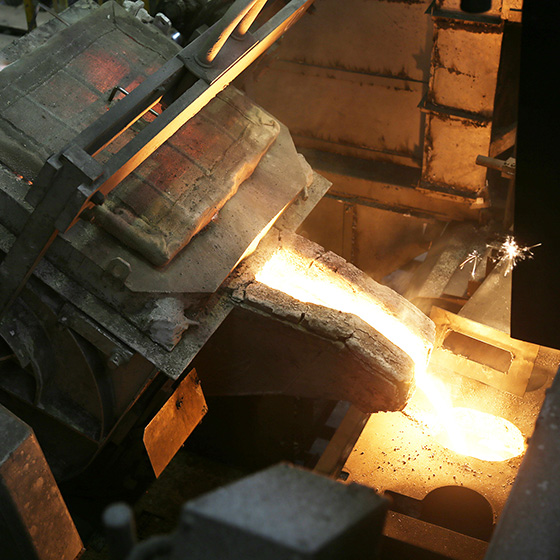
Cooling, flask removal, and shot blasting (sand shake-out)
After a certain period of cooling time suitable for the hardness of the product, the product is separated from the sand mold (flask removal) and the sand is removed from the product by striking iron particles against it through shot-blasting.
Deburring and finishing
Our in-house-developed “Barinder” has functions of a high-precision NC machine tool. It enables the finishing precision – and at a low cost – as required by the customer.
Heat treatment
Heat treatment is given to relieve stress inside the cast product and to adjust hardness. At Koyama, heat treatment of excellent combustion efficiency is possible thanks to the adoption of a waste heat recovery burner.
Washing process
We use a water-blaster nozzle and a robot nozzle to remove sand adhered to the product’s interior surface.
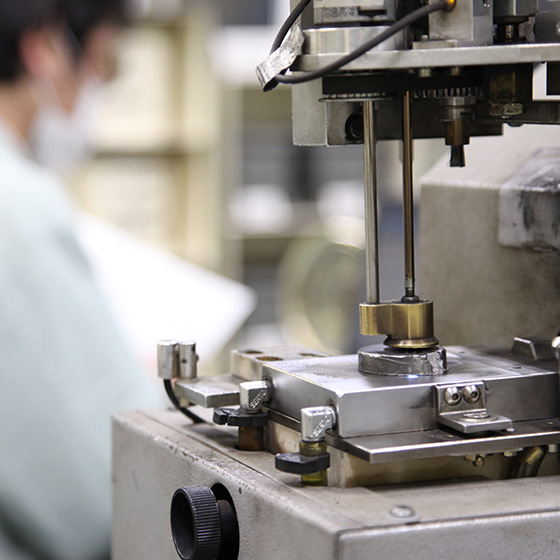
Inspection
In addition to process-by-process quality inspection, we also conduct pre-shipment inspections based on the strictest standards, which include shape measuring as well as non-destructive inspections using an endoscope and X-ray.